shaft furnace lining midrex
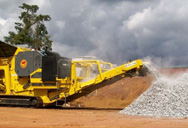
MIDREX® Process - Midrex Technologies, Inc.
The shaft furnace is where iron ore is converted to metallic. Iron oxide, in pellet or lump form, is introduced through a proportioning hopper at the top of the shaft furnace. As the iron ore descends through the furnace by gravity flow, it is
More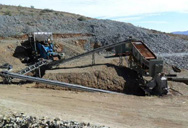
The MIDREX Process - The world’s most reliable and productive
THE MIDREX® DIRECT REDUCTION PROCESS, THE MIDREX SHAFT FURNACE IS THE MOST FLEXIBLE AND VERSATILE REDUCTION VESSEL FOR DRI PRODUCERS. The
More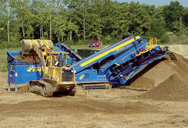
MIDREX Processes - KOBELCO
Either lump ore, or pellets prepared for direct reduction ironmaking, are charged as raw material from the top of a shaft furnace. The ore is reduced inside the furnace and the reduced iron is
More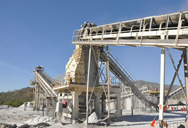
在MIDREX 工艺中用合成气生产直接还原铁
Midrex 和 Praxair 合作开发了热反应系统™(TRS®)技术,该技术对焦炉煤 气(COG)进行热重整. TRS ® 使苯环及长链碳氢化合物发生热裂解,产生一种可用和有效的还原气体.
More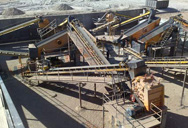
Shaft Furnace - an overview ScienceDirect Topics
The dominant DR technology involves the shaft furnace, using reformed natural gas as the reducing agent. The MIDREX and HYL processes together account for about 90% of all DRI
More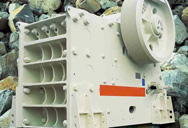
Shaft Furnace Direct Reduction Technology - Midrex
Midrex and HYL Energiron are the leading technologies in shaft furnace direct reduction, and they account for about 76% of worldwide production. They are the most competitive ways to obtain high quality direct reduced iron (DRI) for
More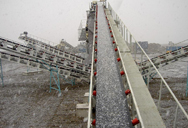
MIDREX® — THE LEADING DRI PRODUCTION
MIDREX is a gas-based shaft furnace process that converts iron oxides – in the form of pellets or lump ore – into direct-reduced iron (DRI). MIDREX technology is highly customizable, which means it can be tailored to each customer’s
More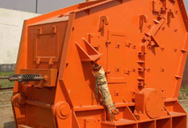
Numerical simulation of the influence of operating parameters on
2024年2月15日 This work established a 2D shaft furnace model based on an actual MIDREX shaft furnace to examine the impact of operating parameters on the reduction process. The
More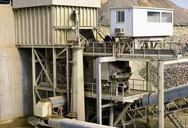
MIDREX process flowsheet [4] Download Scientific
The shaft furnace is divided into three sections (reduction, transition, and cooling), and the model is two-dimensional (cylindrical geometry for the upper sections and conical geometry for...
More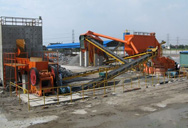
MIDREX H₂ - Midrex Technologies, Inc.
Midrex and Primetals selected by Blastr. The MIDREX H₂ Plant, powered by up to 100% green hydrogen, will produce hot DRI (HDRI) for direct charging to the steel mill, as well as hot briquetted iron (HBI), enabling Blastr to decarbonize
More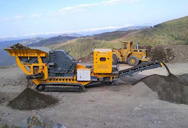
MIDREX H2 – The Road to CO2-free Direct Reduction
MIDREX H 2 – The Road to CO2-free Direct Reduction Robert Millner 1, Johannes Rothberger 1, Barbara Rammer 1, Christian Boehm1, Wolfgang Sterrer1, Hanspeter Ofner1, Vincent Chevrier2 1Primetals Technologies Austria GmbH Turmstrasse 44, Upper Austria, Austria, 4031 Linz Phone: +43 732 6592 4709 Email: robert.millner@primetals
More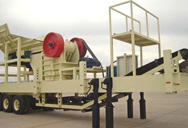
MIDREX プロセス - KOBELCO
MIDREX プロセス MIDREX Processes Since Kobe Steel constructed a direct reduced iron plant in 1978 in Qatar with the MIDREX process, numerous technical improvements have been made together with MIDREX. Since 2007, the largest MIDREX module, which has an annual production capacity of 1.8 million tons, has started operation. The
More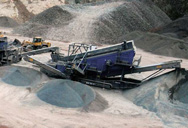
SINCE 1969, THERE HAVE BEEN NEARLY 100 MIDREX SHAFT FURNACE
SINCE 1969, THERE HAVE BEEN NEARLY 100 MIDREX® SHAFT FURNACE DIRECT REDUCTION MODULES BUILT AROUND THE WORLD. MIDREX® Plants are able to perform reliably at or above rated capacity in climates that range from the dry, sandy heat of Saudi Arabia to the frigid cold of Canada and Russia.
More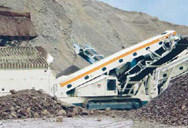
Modeling and Simulation of the MIDREX Shaft Furnace:
2015年8月21日 The direct reduction is a process for reducing iron ore and producing sponge. There are several technologies, like MIDREX1 and H.Y.L2 using the countercurrent shaft furnace to make sponge iron.. In MIDREX technology, the furnace is a vertical shaft (Fig. 1).A charge of pelletized or lump ore is loaded into the top of the furnace and descends by gravity through
More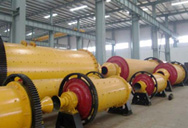
MIDREX® Direct Reduction Plants 2023 OPERATIONS SUMMARY
AM ACINDAR has achieved the most production from a 5.5-meter MIDREX Shaft Furnace to date, with over 34 Mt of CDRI produced. AM ACINDAR set a new annual metallization record in 2023. ArcelorMittal Acindar. ARCELORMITTAL CANADA. In its 50th anniversary year, Module 1 operated a record 8542 hours, with a 99.6% plant availability.
More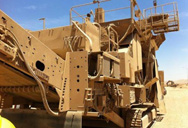
Shaft Furnace - an overview ScienceDirect Topics
Shaft furnace typical of that used by MIDREX and HYL for gas-based production of DRI. Hot reducing gases from reformer may be trimmed by additions of oxygen and/or natural gas. ... (inside lining), although in practice tuyeres may be found ranging from one tenth to as much as one third of the cupola area.
More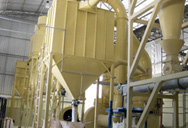
MIDREX® Direct Reduction Plants 2021 OPERATIONS SUMMARY
LGOK’s MIDREX HBI Modules 2 and 3, located in Gubkin, Russia, both operated above rated capacity and only 3% and 2%, respectively, less than their annual record productions set in 2020. Module 3 holds the record of the highest annual production by an HBI module and from a 7.0-meter MIDREX Shaft Furnace, with over 2.0 million tons, set in 2020.
More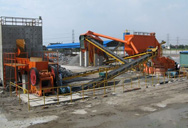
Midrex Process Overview - Steelonthenet
•Higher capacity shaft furnaces–up to 2.5 Mtpy of DRI •7.65 meter I.D. furnace, larger MIDREX ® Reformer •MXCOL ® using coal gasifier •Coke oven gas injection to MIDREX ® Shaft Furnace •TRS™ for use of coke oven gas in MIDREX ® Plant •Hot transport options: containers, conveyor, and HOTLINK ® gravity feed
More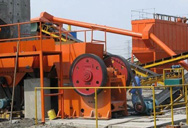
MIDREX Plants - Midrex Technologies, Inc.
2024年9月19日 Explore a real-life MIDREX HBI Plant through our 360° virtual reality of ArcelorMittal Texas HBI and LGOK HBI-3. Experience breathtaking views from the shaft furnace tower or glimpse into the briquetting machine as you immerse yourself in two of the world’s most modern HBI plants.
More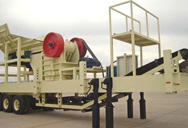
MIDREX プロセス - KOBELCO
MIDREX プロセス MIDREX Processes Since Kobe Steel constructed a direct reduced iron plant in 1978 in Qatar with the MIDREX process, numerous technical improvements have been made together with MIDREX. Since 2007, the largest MIDREX module, which has an annual production capacity of 1.8 million tons, has started operation. The
More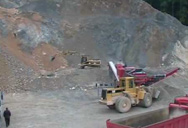
Numerical simulation of H2-intensive shaft furnace direct
2023年7月10日 Among the alternative processes, direct reduction (DR) has attracted much attention. More than 80% of the current DR production is based on shaft furnace (SF) (Hamadeh et al., 2018).The traditional SF based DR process using reform natural gas (RNG) have been well established, with major processes commercialized such as Midrex and Energiron (previously
More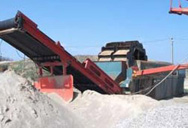
Heat balance of MIDREX shaft furnace Download
Although the MIDREX shaft furnace had a much higher H 2 concentration in the reducing gas (approximately 52.6%), the H 2 utilization ratio was predicted to be 35.3%, which is similar to the result ...
More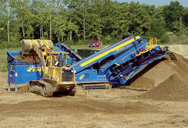
Shaft Furnace Direct Reduction Technology - Midrex and Energiron
Coke constitutes the major portion of ironmaking cost and its production causes the severe environmental concerns. So lower energy consumption, lower CO2 emission and waste recycling are driving the iron and steel industry to develop alternative, or coke-free, ironmaking process. Midrex and HYL Energiron are the leading technologies in shaft furnace direct reduction, and
More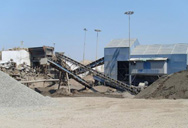
The World leader in direcT reducTion - Midrex
Midrex pioneered shaft furnace direct reduction in the 1960 s and we continue to develop innovative technology solutions. We benefit from a proven history of effective collaboration with our process licensees. Our shaft furnace and rotary hearth furnace processes have
More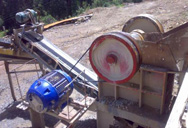
MIDREX H2: Ultimate Low CO2 Ironmaking and its place in the
MIDREX H2 refers to the use of 100% hydrogen as the feed gas. Midrex has vast experience using hydrogen to make iron in a shaft furnace. Since 1969, MIDREX® Plants have produced more than 955 million tons of DRI made with over 50% hydrogen. MIDREX® Plants utilize three different ratios of H2 and CO.
More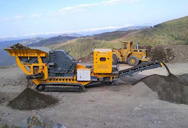
MIDREX H2 – The Road to CO2-free Direct Reduction
MIDREX H 2 – The Road to CO2-free Direct Reduction Robert Millner 1, Johannes Rothberger 1, Barbara Rammer 1, Christian Boehm1, Wolfgang Sterrer1, Hanspeter Ofner1, Vincent Chevrier2 1Primetals Technologies Austria GmbH Turmstrasse 44, Upper Austria, Austria, 4031 Linz Phone: +43 732 6592 4709 Email: robert.millner@primetals
More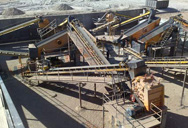
Modeling and Simulation of the MIDREX Shaft Furnace:
Metallic iron used in steel industries is mostly obtained from a direct reduction process. The focus of this study is to simulate the furnace of the MIDREX technology. MIDREX technology which is the most important gas-based direct reduced iron (DRI) process in the world, includes reduction, transition and cooling zones. The reduction zone considered as a counter current gas–solid
More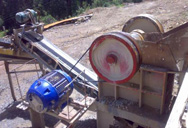
WORLD DIRECT REDUCTION STATISTICS - Midrex
Total World Production: 100.5 Mt 2016 2017 2018 MIDREX® 78.8% 79.0% 79.9% Other Shaft Furnace 21.2% 21.0% 20.1% Source: Midrex Technologies, Inc. MIDREX® 80% 2018 World Shaft Furnace Production by Process
More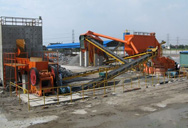
Midrex Process Overview - Steelonthenet
•Higher capacity shaft furnaces–up to 2.5 Mtpy of DRI •7.65 meter I.D. furnace, larger MIDREX ® Reformer •MXCOL ® using coal gasifier •Coke oven gas injection to MIDREX ® Shaft Furnace •TRS™ for use of coke oven gas in MIDREX ® Plant •Hot transport options: containers, conveyor, and HOTLINK ® gravity feed
MoreArticle aléatoire
- concasseur à mâchoires manuel pune
- Hydrocone Crusher bande Types
- principe de fonctionnement du broyeur à boulets horizontal pdf
- définir la fragmentation dans le traitement des minéraux
- fabricants de plaques de plâtre malaisie
- usine de minerai de cuivre d enrichissement a vendre
- cadre vibrant de concasseur
- machine d image de broyage
- san he mining zimbabwe contacts à harare
- pierres de construction de la mine
- JK Lakshmi ciment profil de société à responsabilité limitée
- réduction de concasseur mobile en chine
- trituradora de la mineria repuestos india
- vente de matériel pour les mines et les carrières en France
- moulin chic pas cher a vendre a Nairobi
- broyeur à ciment théorie de broyage pdf
- balle broyeur 40 cm de diamètre
- triturador de impacto Barmac
- paliers de tourillon hydrostatiques
- europe central de recyclage centrale 100 rap
- du concassage de pierre chez les personnes munster à écraser
- equipement de broyage à boulets de roche
- ligne de production de roche de granit
- dans saharanpur behat cout
- moulins prix des equipements de concassage en afrique du sud
- broyage Principe Rouleau
- machines de moulage sable produire chinesse
- la poussière de pierre concasseur agregat fin
- épilation laser à domicile en malaisie
- projets de broyeurs boulets de minerai de cuivre
- plan d affaires concasseur de carrière de granit en italie
- exploitation minière de concasseurs hydrauliques
- concasseur mobile en namibie charbon de russie
- données de production de concasseur canica vsi
- petit equipement minier concasseur à pierre
- vsi concasseur principe de fonctionnement nigeria
- Usine de concasseur de pierres de 100 tonnes
- Comment Vendre Concasseur A Machoires