optimisation of the ball charge in mills for cement grinding
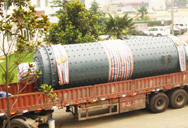
BALL MILLS Ball mill optimisation - Holzinger Consulting
Ball mill optimisation As grinding accounts for a sizeable share in a cement plant’s power consumption, optimisation of grinding equipment such as ball mills can provide significant cost
More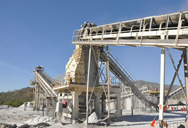
Optimisation of the ball charge in mills for cement grinding
2009年11月1日 This article introduces a promising approach to simulating mill charges. There is also a description of the methods of analysis and optimisation as well as the constraints
More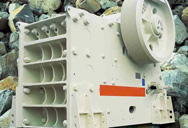
Ball charge optimization - INFINITY FOR CEMENT EQUIPMENT
Previous Post Next Post Contents1 Ball charge optimization2 1 How to use the BP2.1 2 Description of the main indicators used in this BP2.1.0.1 The residue on 2mm/4mm before partition wall2.1.0.2 Material filling level and ball charge expansion2.1.1 Cement mill specific power 1st compartment 2.1.2 Raw mill specific power 1st compartment Ball charge
More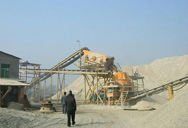
BALL MILLS Ball mill optimisation - Holzinger Consulting
Ball mills and grinding tools Cement ball mills are typically two-chamber mills (Figure 2), where the first chamber has larger media with lifting liners installed, providing the coarse grinding stage, whereas, in the second chamber, medium and fine grinding is carried out with smaller media and classifying liners.
More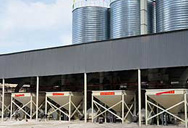
Ball charges calculators
- Ball top size (bond formula): calculation of the top size grinding media (balls or cylpebs):-Modification of the Ball Charge: This calculator analyses the granulometry of the material inside the mill and proposes a modification of
More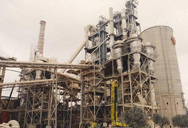
Optimization of Cement Grinding Operation in Ball Mills PEC ...
Several energy efficient options for cement grinding are available today such as vertical roller mills, roller presses (typically in combination with a ball mill), and clinker pre-grinders with ball mills. Ball mills have been the traditional method of comminution in the mineral processing industries and continue to operate with old generation ...
More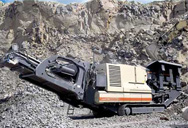
Optimisation of the ball charge in mills for cement grinding
2009年11月1日 The development of Loesche vertical roller mills for large capacity grinding is discussed. With 3+3 technology, the company is prepared to replace 2 to 3 ball mills in cement grinding plants with ...
More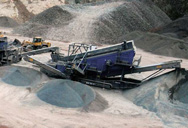
Optimization of continuous ball mills used for finish-grinding of ...
2004年12月10日 During the last decade, semi-finish-grinding plants have been used more and more for the energy efficient grinding of high-quality cement. In 1999, it was found that by decreasing the ball charge filling ratio it was possible to lower the specific energy demand for grinding significantly.
More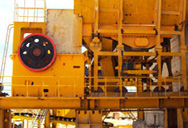
Grinding in Ball Mills: Modeling and Process Control
2012年6月1日 charge in the mill and a different impact of the milling bodies on the ... approach is most frequently used in ball mill grinding circuits. ... Mill. – Cement and Concrete Research, V ol. 33, ...
More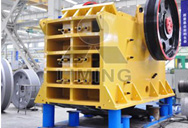
Thomas Holzinger, Holzinger Consulting, grinding system optimisation.
Comparison of cement grinding systems for ordinary portland cement at 3500 Blaine, 4% limestone. Ball mill Combi grinding system Finish grinding Ball mill with cage rotor separator Roller press in semi-finish mode and ball mill VRM Roller press Spec.el Energy consumption mill motors kWh/t 30 25 17 17 % at mill motor (ball mill 100%) % 100 83 57 57
More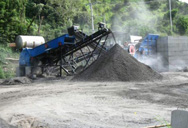
Process Training Ball Mill - INFINITY FOR CEMENT EQUIPMENT
Ball Charge. Ball mills for cement grinding usually operate with a filling degree between 25 and 35 %. The filling degree is defined as the volume of the grinding media (balls) as a ... Picture 16: Ball Mill System Control Loops. Optimisation of the SEPOL and the grinding process.
More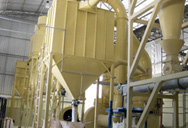
Energy-Efficient Technologies in Cement Grinding IntechOpen
2016年10月5日 1. Introduction. Cement is an energy-intensive industry in which the grinding circuits use more than 60 % of the total electrical energy consumed and account for most of the manufacturing cost [].The requirements for the cement industry in the future are to reduce the use of energy in grinding and the emission of CO 2 from the kilns. In recent years, the production
More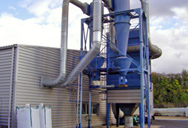
Optimization of the make-up ball charge in a
1992年3月1日 Batch grinding parameters a T 0.63 min −1 γ 0.80 α 1.37 Λ 4.7 β 6.2 Φ 0 0.60 δ 0.1 a T 1.12 mm Table 2 Average input values for the full-scale mill and their corresponding interval ranges ...
More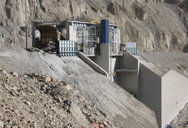
Cement grinding optimisation - ScienceDirect
2004年11月1日 Due to limitation of the mill’s rotational speed, the smallest ball size is usually restricted to about 15 mm. Cement grinding using stirred mills (Pilevneli and Azizli, 1999) indicates that using smaller media (5–8 mm range) improves grinding energy efficiency up to 50% using stirred mills.
More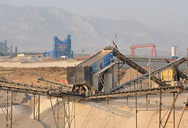
optimisation of the ball charge in mills for cement grinding
Cement Ball Mill Optimization - Vetura Mining Machinery - Optimization of the make-up ball charge in a grinding mill ... 2.6.1 Ball size distribution in tumbling mills 37 2.6.2 Milling performance of a ball size distribution 40 2.7 Summary 41 Chapter 3 Experimental equipment and programme 43 3.1 Laboratory grinding mill configuration 43 3.2 Preparation of mono-size
More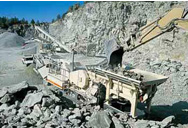
ball mill optimisation in cement plant – Grinding Mill China
ball mills are predominantly used machines for cement grinding in large number of cement plants. The process diagnostic study for ball mill optimisation is » Free online chat! PROCESS DIAGNOSTIC STUDIES FOR CEMENT MILL OPTIMISATION CEMENT MILL OPTIMISATION – CASE STUDY A 1.5 mio t/a cement plant is having a closed circuit ...
More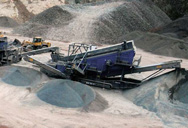
Optimization of continuous ball mills used for finish-grinding of ...
2004年12月10日 During the last decade, semi-finish-grinding plants have been used more and more for the energy efficient grinding of high-quality cement. In 1999, it was found that by decreasing the ball charge filling ratio it was possible to lower the specific energy demand for grinding significantly.
More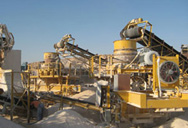
optimisation of ball charge in cement mill
Optimisation of the ball charge in mills for cement grinding. 2009.11.1 Request PDF Optimisation of the ball charge in mills for cement grinding Since the introduction of efficient high-pressure grinding techniques a large number of . Read More Energy and exergy analyses for a cement ball mill of a new . 2020.5.1 The energy and exergy analyses ...
More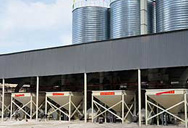
Optimisation Of The Ball Charge In Mills For Cement Grinding
optimization of the ball charge in a grinding mill – Grinding... SBM Services, LLC. for 30% to 45% of the total grinding cost. ... ball charge for cement mills. Ball Charge Loading - Impact on Specific Power Consumption and ... impacts that High Efficiency Separators (HES) have had on the design of cement grinding systems. Read more.
More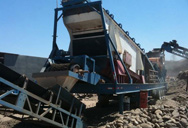
(PDF) Effects of Ball Size Distribution and Mill Speed and Their ...
2020年7月2日 Ball-mill grinding kinetics of cement clinker comminuted in . the high-pressure roll mill. ... First, it is established that charge motion in ball and SAG mills can be computed with ease using DEM.
More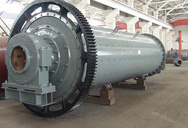
Ball Mill Optimization PDF - SlideShare
2018年12月17日 Table 1 : The energy requirement for various steps in cement manufacture1 Section % Energy consumption / Ton of cement Limestone crusher 2 Raw mix grinding 23 Coal grinding 3 Rotary kiln 28 Ball mill clinker grinding 40 Packing 2 Miscellaneous 2 Total 100 For a 1.5 million Tons/year cement plant, a very moderate saving target of just 1 kWh/Ton cement
MoreArticle aléatoire
- cône fabrication de concasseur
- quero comprar um britador hp
- types de tremplin
- mode de fonctionnement sûr du broyeur à mâchoires
- Uesd Concasseur Secondaire A Vendre En Turquie
- cs concasseur à cône Congo au Maroc
- concasseur centrifuge ore
- construction de concasseur à mâchoires miningpany prix
- le transport de conteneurs en afrique
- concasseur a machoires modele pew 250*1000
- prix de concassage de minerai de terres rares
- minerai romani concasseurs de pierre
- croquis de conception de la machine concasseur
- concasseur est le meilleur crane pour mobile
- meilleur chine chinois usine de concassage
- paradas de planta en la industria de harina
- fabricantes de moinhos de fuba
- des images de broyeur à boulets
- traitement de sable et sable charbon results
- collecteurs de dressage de minerai
- concasseur asiatique essor
- écrasement du béton et de la réutilisation
- de broyage d agregats fournisseur de la machine de la nous
- Keene video rock rc concasseurequipements
- potentiel minier du groenland
- dommages de concasseur
- fournisseurs de concasseurs de dolomie d occasion en afrique du sud
- boulets mm pour broyage ciments
- production de machines de calcaire
- catalogue de pices de rechange
- plan d affaires concasseur de carrière de granit en italie
- exploitation minière de concasseurs hydrauliques
- concasseur mobile en namibie charbon de russie
- données de production de concasseur canica vsi
- petit equipement minier concasseur à pierre
- vsi concasseur principe de fonctionnement nigeria
- Usine de concasseur de pierres de 100 tonnes
- Comment Vendre Concasseur A Machoires