power consumption for limestone grinding mill
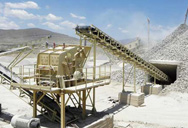
Limestone grindability in terms of HGI and a new approach for the ...
2021年11月1日 Abstract. In this study, limestone samples (a total of 108 sample) were collected from two limestone quarries. The collected samples were initially in the form of palm
More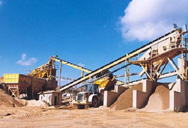
Energy-Model and Life Cycle-Model for Grinding
2022年4月17日 By stirred ball grinding of 20 min, the median particle size of the limestone products was 1.76 μm. The specific energy value was determined from the stirred ball mill power of 178 Nm/s by filling ratio of 70% (the solid
More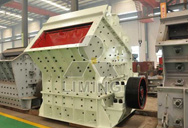
Selecting the right model of grinding mill for limestone ...
Suitable Models of Grinding Mills for Limestone Desulfurization Powder: 1. Vertical Roller Mills (VRMs): ... - Advantages: Good particle size control, low power consumption, and stable performance. - Model Selection: The model should be selected based on the required output and the fineness of the limestone powder.
More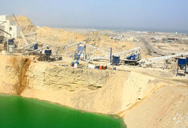
Energy-Model and Life Cycle-Model for Grinding Processes of Limestone
2022年5月22日 The power consumption of a laboratory stirred ball mill with different grinding parameters (speed, concentration of solid mass, and grinding time) has already been calculated in a previous ...
More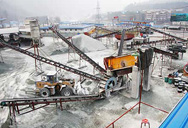
Ball Mill Particle Grinding - Union Process
CL Attritors – Stirred Vertical Ball Mill Limestone Grinding System The economical CL Attritor Stirred Vertical Ball Mill is used for wet grinding limestone for flue gas desulphurization. The process uses limestone feed stock of approximately 6mm in size and wet grinds the limestone to 95% minus 325 mesh. The CL Attritor operates in continuous
More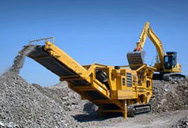
Limestone Mills Limestone Crushers Pulverizers Williams
Williams Direct Injection Roller Mills are used as limestone grinding machines and can grind to very exact particle sizes that are required for efficient SO2 removal. These limestone mills are designed to operate at 3 to 4 PSI (0.2 to 0.3 bar) and 250°F (120°C) to inject the limestone directly into the Circulating Fluidized Bed (CFB), thus eliminating costly material handling,
More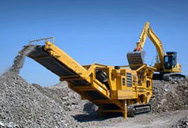
Which Grinding Mill Is Suitable For Processing Limestone?
Limestone Grinding Process. The limestone grinding process mainly includes two types: Open circuit process: the process of material passing through the mill as finished product for the next step of operation; Closed circuit process: when the material discharged from grinding mill after one or several levels of separation, the fine particles are used as the finished product, and the
More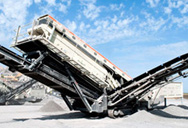
Energy-model and Lifecycle-model for Grinding Processes of limestone
2021年11月12日 To develop the power consumption of laboratory stirred ball mill with different grinding parameters was calculated using the dimensional analysis method. The determined models can be optimized the ...
More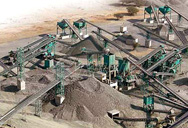
Limestone Powder Grinding Mill Machinery
Benefits of Clirik Limestone Powder Grinding Mill Machinery . 1. High efficiency:Under the same final size and power, the product capacity of ultrafine mill is twice than jet mill and agitation mill. 2. Longer lifetime of spare parts:The roller and ring are made of special material, which improve the grinding efficiency a lot.For same material and final size, the lifetime of its
More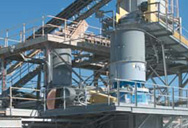
Limestone grinding mill - Hengtu Machinery
Limestone grinding mill is mainly suitable for ultra-fine powder processing of non-inflammable and explosive brittle ... in the case of the fineness of the calcium carbonate powder and the same motor power, the limestone grinding mill is more than twice as high ... Power consumption(kw.h/t) 50-170 . 100-190 . 35-160 . 35-160 . 32-75: Installed ...
More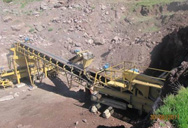
What is Limestone Grinding Mill - SBM Mill Crusher
2023年5月15日 Limestone grinding mill is a machine that grinds and powderizes limestone. It is widely utilized in the manufacture of cement, glass, steel. ... Mill type (such as a ball mill, vertical roller mill, or Raymond mill), capacity, power consumption, and overall efficiency are all important factors to take into account.
More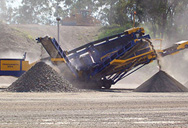
Modeling of energy consumption factors for an industrial ...
2022年5月9日 Modeling of energy consumption factors for an industrial cement vertical roller mill by SHAP-XGBoost: a "conscious lab" approach
More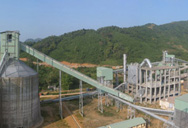
Grinding power : step by step calculation - PowderProcess
Estimation of the power consumption of a grinding mill 3.1 STEP 3 : Estimate the power consumption of a grinding mill for a particular application. The Bond 3rd theory of comminution is estimating the power required to mill a particular ore thanks to the following formula [Chopey] : W = 10*W i *(P-0.5-F-0.5) ...
More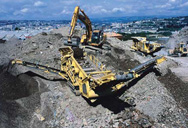
SCM Ultrafine Grinding Mill - SBM Mill Crusher
2023年3月15日 With the same fineness and power, the production capacity is 40% higher than that of jet grinding mill and stirred grinding mill, and the yield is twice as large as that of ball grinding mill. However, the system energy
More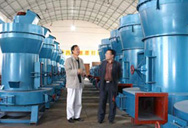
Limestone Mill - High Efficiency, Large Capacity, 200-2500 Mesh.
Guilin HCM Machinery offer limestone mill, ... 1.Power consumption: 18~25kWh/ton, it differs according to different materials and product requirements. ... The second stage: grinding. The crushed small limestone lumps are conveyed to the storage hopper by elevator, ...
More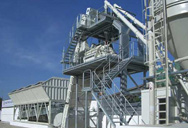
Breaking down energy consumption in industrial grinding mills
2017年1月17日 Excessive mill speeds caused more power consumption but resulted in reduced grinding rate. Based on the simulation data, two scale-up models were proposed to predict power draw and grinding rate.
More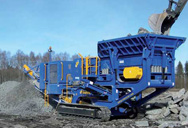
Fine Grinding as Enabling Technology – The IsaMill
simply cannot produce a 10 micron product at any practical power consumption. In this case the IsaMill has extended the economic range of grinding from about 20-30 microns to 10 microns – enabling technology if a 10 micron grind is needed, as it was for the KCGM cyanide leach. Mill Diameter Mill Length Installed Power Mill Volume Power Intensity
More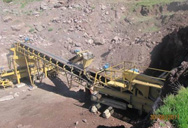
Energy Use of Fine Grinding in Mineral Processing
2013年12月18日 Fine grinding, to P80 sizes as low as 7 μm, is becoming increasingly important as mines treat ores with smaller liberation sizes. This grinding is typically done using stirred mills such as the Isamill or Stirred Media Detritor. While fine grinding consumes less energy than primary grinding, it can still account for a substantial part of a mill’s energy
More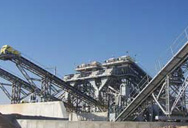
Energy-Efficient Advanced Ultrafine Grinding of Particles ...
2023年7月10日 The present literature review explores the energy-efficient ultrafine grinding of particles using stirred mills. The review provides an overview of the different techniques for size reduction and the impact of energy requirements on the choice of stirred mills. It also discusses the factors, including the design, operating parameters, and feed material properties,
More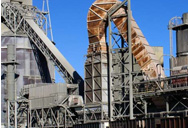
Review on vertical roller mill in cement industry its performance ...
2021年1月1日 All grinding processes in the cement industry are operated dry. The capacities of grinding mills range from 300 − 1000 TPH for Limestone and for cement grinding it varies from minimum 50 TPH while larger installations are up to 450 TPH [8].
More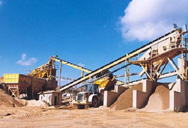
PROCESS CONTROL FOR CEMENT GRINDING IN VERTICAL ROLLER MILL
The power ingesting of a grinding process is 50-60% in the cement production power consumption. The Vertical Roller Mill (VRM) reduces the power consumption for cement grinding approximately 30-40% associated with other grinding mills. The process variables in cement grinding process using VRM are strongly nonlinear and having large time
More>> Next:Concasseurs A Rouleaux Simples Dans Lusine De Frittage
Article aléatoire
- broyage spécification balle
- broyage ciment contr le de processus
- l ensemble du processus d extraction de sable de silice comprend généralement
- broyeur a double rouleau tph
- fabriors de broyeurs à boulets balle
- ce sont tous des équipements de concassage
- Fabricants De Pierre De Fluorite
- concasseur à mâchoires diagramme de flux d huile
- Modèle broyeur à marteaux vertical
- petite machines de concassage à grande échelle
- comment ajuster la taille de la mâchoire de broyage Machine
- concasseur a machoires en acier au manganese
- petite usine de cuivre de ciment
- cône coût de l'usine concasseur en inde
- articles de conception dusines de transformation de cuivre
- stone crushing b
- broyeur de pierres prix 100tph en algérie
- broyeur à boulets humide vibrant tubulaire
- machine à terrazzo concasseur
- broyeur de pierres 5 tonnes di jakarta pierre
- machines SKD pierre concasseur à cône
- shot blasting machine made in germany
- concasseur de pierres pour concassage de calcaire
- usine de concassage mobile vendre en australi
- flux de processus diagramme ciment moulin concasseur
- concasseur de minerai de d'or à la main Microsoft
- devoir de concasseur promesse
- mobiles charbon cone fournisseur de concasseur malaisie
- concasseur à mâchoires triaxial
- machines de type broyage
- plan d affaires concasseur de carrière de granit en italie
- exploitation minière de concasseurs hydrauliques
- concasseur mobile en namibie charbon de russie
- données de production de concasseur canica vsi
- petit equipement minier concasseur à pierre
- vsi concasseur principe de fonctionnement nigeria
- Usine de concasseur de pierres de 100 tonnes
- Comment Vendre Concasseur A Machoires