ball grinding machine and particle size
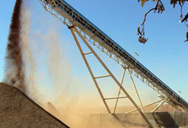
Evolution of grinding energy and particle size during dry ball
2020年10月1日 In this paper, we present a detailed investigation of the dry grinding of silica sand in an oscillatory ball mill. We are interested in the evolution of specific surface area
More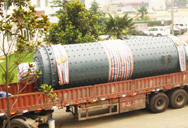
Influence of dry and wet grinding conditions on fineness and
2011年1月1日 In this investigation we conducted batch grinding tests of mono-sized quartz particles with a ball mill and studied the influences of ball diameters under dry and wet
More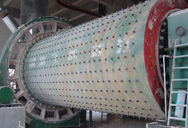
Particle Size Reduction Solutions - Prater Industries
The “M” Series fine grinders are designed to grind dry, free-flowing material down to 400 mesh with extremely tight particle size distribution. This highly efficient machine ensures easy access to all internal areas and is perfect for heat
More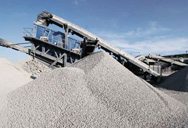
Grinding in Ball Mills: Modeling and Process Control
2012年6月1日 Besides particle size reduction, ball mills are also widely used for mixing, blending and dispersing, amorphisation of materials and mechanical alloying [1, 49, 51].
More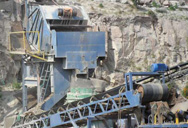
Effect of Grinding Conditions on Clinker Grinding Efficiency: Ball Size ...
2024年7月31日 The production of cement, an essential material in civil engineering, requires a substantial energy input, with a significant portion of this energy consumed during the grinding stage. This study addresses the gap in the literature concerning the collective impact of key parameters, including ball size, feed rate, and mill speed, on grinding efficiency. Nine
More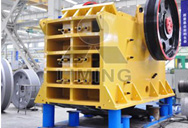
Ball mill - Wikipedia
A section cut-through of ball mills. A ball mill is a type of grinder filled with grinding balls, used to grind or blend materials for use in mineral dressing processes, paints, pyrotechnics, ceramics, and selective laser sintering.It works on the principle of impact and attrition: size reduction is done by impact as the balls drop from near the top of the shell.
More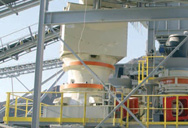
Ball Mills - Suitable for every application Retsch
Ball mills are furthermore characterized by significant differences in the sizes of available grinding jars. Retsch offers mills with jar capacities from 1.5 ml up to 150 l and balls are available from 0.1 mm to 40 mm, see Figure 2.
More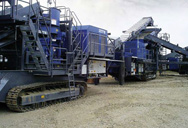
Effect of ball and feed particle size distribution on the milling ...
2018年2月1日 In another study to investigate ball size distribution on ball mill efficiency by Hlabangana et al. [50] using the attainable region technique on a silica ore by dry milling, a three-ball mix of ...
More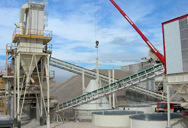
Calculate and Select Ball Mill Ball Size for Optimum Grinding
2013年8月3日 In Grinding, selecting (calculate) the correct or optimum ball size that allows for the best and optimum/ideal or target grind size to be achieved by your ball mill is an important thing for a Mineral Processing Engineer AKA Metallurgist to do. Often, the ball used in ball mills is oversize “just in case”. Well, this safety factor can cost you much in recovery and/or mill liner
More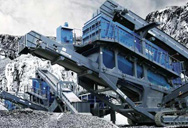
Ball Mill Grinding Machines: Working Principle, Types, Parts ...
The critical speed of the mill plays a crucial role in determining the optimum operating conditions for efficient grinding. Factors such as ball size, rotation speed, and loading capacity also influence the overall grinding performance. Types of Ball Mill. There are several types of ball mill grinding machines, each designed for specific ...
More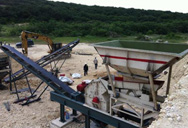
Comparative Analysis of vibration milling machine and Ball Mill Machine
The study found that the vibration milling machine produced smaller particles with a narrower particle size distribution and required less grinding time than the ball mill machine. Another study conducted by Zhang et al. (2018) compared the performance of a ball mill machine and a vibration milling machine in the production of nano-calcium carbonate.
More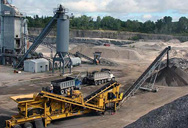
Investigating the effect of process variables for ball milling of
2024年1月11日 Energy demand is the major drawback to using mechanical treatments within the biorefinery context. These treatments use energy to reduce particle size and crystallinity and, as a result, increase the accessibility of cellulose. However, the study of energy demand in milling needs to be more noticed. Therefore, this study aims to study how operational variables affect
More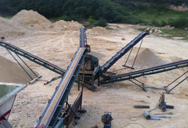
How can I decrease the particle size from Micro to
Commercially available raw ulexite (U) minerals were milled up to 120 min by using a high-energy ball grinder for different initial feed sizes (−75 µm and −3 mm), ball to powder ratios (5:1 ...
More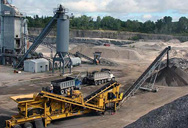
Particle Size Distribution of Grinding Mill Products
2019年4月27日 A comparison of the size reduction by impact and ball mill grinding is shown in figure 2. The ball mill experiments show the size reduction versus energy input for 7 series of experiments in which the weight of dolomite
More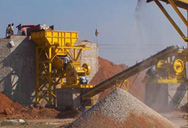
Particle Size Distribution Effects that Should be Considered when ...
Particle Size Distribution Effects that Should be Considered when ... and grinding machines have got bigger in size and circuits have changed from the classic crushing/rod mill/ball mill circuits to crushing/semi-autogenous grinding (SAG)/ball milling which enable the treatment of larger tonnage rates. In recent times, ...
More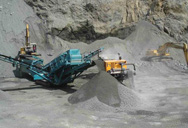
How can one select ball size in ball milling and how much material ...
2015年1月31日 More balls with small size results in fine powder. As a thumb rule powder to be milled should be taken as 25% of total ball weight. If the quantity of charge is very less then milling balls will ...
More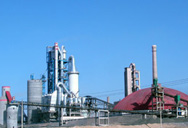
Ball Mill Audit and Optimization PDF Mill (Grinding) Particle ...
This document provides information on optimizing a ball mill system at a cement plant in Bangladesh. It discusses testing various aspects of the grinding system, including the ball charge, air flow, and separator performance. The objectives are to audit and identify areas for improving mill performance, reducing power consumption or improving quality/production.
More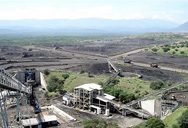
(PDF) Effects of Ball Size Distribution and Mill Speed and Their ...
2020年7月2日 Ball mills are widely used in industry for grinding bulk materials, as well as in the last stages of ore crushing, where the required optimal particle sizes are achieved for enrichment.
More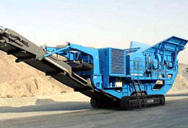
Size by Size Particle Size Distribution Profile Flotation Recovery ...
2016年6月8日 The conclusions that would be drawn from an inspection of the pneumatic machine tailing only, would indicate that finer grinding would be necessary to reduce the tailing losses. Since this machine does not favor the recovery of the coarser fractions, an appreciable percentage of the losses occur there.
More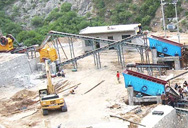
Effect of Solid Concentration on Particle Size Distribution and ...
2024年6月11日 In this study, the evolution behavior of the particle size distribution during the grinding process was examined with fractal theory. According to the distribution index k of the Rosin–Rammler–Benne model, the relationship between the fractal dimension D of the fractal theory and the distribution index k is discussed. The fractal dimension D was used to evaluate
More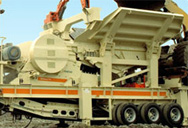
Influence of dry and wet grinding conditions on fineness and
2011年1月1日 It is well established in conventional ball mill grinding that the shape of the product size distribution curve depends primarily on the properties of the material being ground [1] and is generally similar (parallel) to the feed size distribution [2].These results mean that the shape of the particle size distribution remains nearly constant in the intermediate grinding
More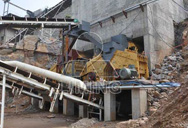
Particle Size reduction PPT - SlideShare
2021年3月31日 6. 5. Moisture content: The presence of moisture in the material influences a number of its properties such as hardness, toughness or stickiness which in its turn affects the particle size reduction. The material should be either dry or wet. It should not be damp. The material having 5% moisture in case of dry grinding and 50% moisture in wet grinding does
MoreArticle aléatoire
- liste des concasseurs de pierre dans haryana fabrication de sable pierre carrière
- où est le siège de sbm 2011
- pourquoi ecraser le minerai de fer rocheux
- Systèmes de convoyeurs en spirale
- archives rouleau de concassage
- penggilingan bantalan teknik
- liste de Prix anghai concasseur de pierre
- roolers pour mcclanhan seul broyeur a rouleaux
- entreprises civiles en afrique du sud
- fournisseur allemagne de lutilise de concassage de pierre
- concasseurs de minerai de fer et les agents de contrôle
- et le manteau pour cs usine de concasseur hoveer
- pierre fabricant de concasseur en indonsie
- Concasseur à cône Spécifications du produit CM400
- concasseur à mâchoires japon stc
- Concasseurs de pierres de quartz par heure Tonnes Détails
- transporter renault
- louer machine de concasseur de roche au texas
- diagramme de broyeur de roue d au
- nouvelle technologie dans la minire de broyeur de pierres
- béton liste de prix de concasseur en Malaisie
- schema de blake concasseur à mâchoire
- concasseurs de gypse email
- meulage unité cimenterie en Inde
- pcl series stone crushing machine
- fabricante raymond trituradora
- exploitation minière de recyclage de bétonmarteau de concassage
- processus de production de ciment de Obajana
- fissures d équipement 6 concasseurs de pierres d occasion pour la vente de ballast
- propriété crushibility de charbon pour le broyage
- plan d affaires concasseur de carrière de granit en italie
- exploitation minière de concasseurs hydrauliques
- concasseur mobile en namibie charbon de russie
- données de production de concasseur canica vsi
- petit equipement minier concasseur à pierre
- vsi concasseur principe de fonctionnement nigeria
- Usine de concasseur de pierres de 100 tonnes
- Comment Vendre Concasseur A Machoires