how to carry out maintenance of cement mill in cement
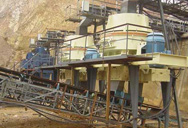
MAINTENANCE IN THE CEMENT INDUSTRY
Key Maintenance Functions. There are a few key functions in maintenance that must be developed and should be part of an organization to achieve the overall targets and strategy. Work execution; Work supervision; Work planning
More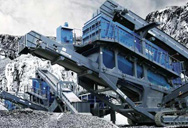
Analysis of Raw Mill Machines Maintenance in Cement Industry
2020年5月30日 To find out the frequency of damage to the machine or the time interval between damage to the tool (MTBF) and the length of time used to repair the tool (MTTR), the Total
More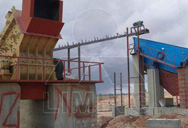
The Cement Plant Operations Handbook - International Cement
In combination with cement storage, there should be adequate storage capacity for clinker and other cement components to maintain deliveries during maintenance shutdowns and, if the
More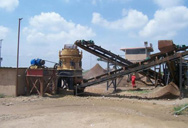
Maintenance Analysis of Raw Mill Machines in Cement
2024年2月22日 Cement production data for CC-2 raw mill machines are taken in the form of average cement production data in tons, where raw materials are distributed using a belt conveyor which then goes through a mixing process on
More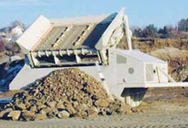
Continuous improvement of maintenance process for the cement
2014年10月7日 Continuous maintenance improvement (CMI) is an ongoing effort to improve maintenance aimed at maintenance process simplification and reduction or elimination of
More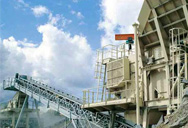
Analysis of Raw Mill Machines Maintenance in Cement Industry
2020年5月1日 To find out the frequency of damage to the machine or the time interval between damage to the tool (MTBF) and the length of time used to repair the tool (MTTR), the Total
More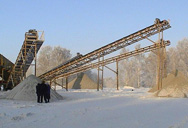
Analysis of Raw Mill Machines Maintenance in Cement Industry
Maintainability is a business and costs to carry out maintenance (maintenance). A measure of maintainability is Mean Time To Repair (MTTR), the increase of MTTR identifies the decrease of
More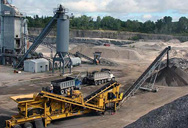
Maintenance Practices in Cement Industry - ResearchGate
Khan and Darrab [1] reported that the purpose of maintenance is not only to upkeep the plant machinery and equipments preventing from failure and breakdowns, increasing reliability,...
More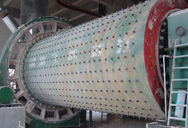
Cement Mill Optimization: Practical Strategies for
Optimizing the operation of cement mills is essential to maximize productivity, reduce energy consumption, and improve the quality of the final cement product. In this article, we will delve into practical strategies for cement mill
More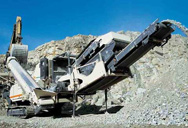
The Cement Plant Operations Handbook - International Cement
ASTM cement types and specifications – 16. European EN 197 cement specification – 17. Composite cements (intergrinds and blends) – 18. Supersulphated cement – 19. Calcium aluminate cement (CAC) – 20. Shrinkage-compensating cements (SCC) – 21. ISO 9001:2000 Quality 8. Maintenance168 1. Maintenance benefits and costs – 2. Failure ...
More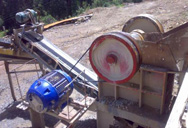
Impacts of Cement Production on the Environment with Practical
clinker are processed in the mill, divided into two stages: the grinding stage in chamber I and the milling stage in chamber II. In the final stage, the cement is transferred to the separation stage, where the raw material is returned to the mill while the fine cement is stored in the storage silo [38, 40]. 2.3 Cement Packaging and Dispatch
More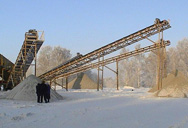
Cement Ball Mill Maintenance - INFINITY FOR
BALL MILL INSPECTION PROCEDURE. source : thecementgrindingoffice Introduction. This document is intended to help the staff of the cement plants. On a process point of view, a mill inspection is
More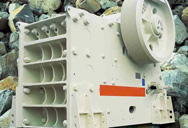
Improvements in New Existing Cement Grinding Mills by Tim
o For ball mills, only 3 – 6% of absorbed energy is utilized in surface production, the heat generated can increase mill temperature to > 120⁰ C causes excessive gypsum dehydration media coating if mill ventilation is poor. Types of cement mills. There are basically 4 types of cement mills in use today: Ball Mill (BM)
More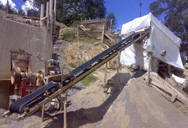
Cement Ball Mill - Cement Grinding Machine - Cement Mill
What Is A Cement Ball Mill. The cement ball mill is a kind of cement grinding mill.It is mainly used for grinding the clinker and raw materials of the cement plant, and also for grinding various ores in metallurgical, chemical, and electric power enterprises.It has the characteristics of strong adaptability to materials, continuous production, a large crushing ratio, and easy-to-adjust the ...
More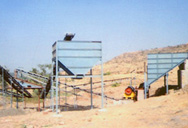
How To Optimize The Operation Of The Cement Mill
2024年1月23日 Conducting routine inspections and proactive maintenance of the cement grinding mill components, such as grinding media, liners, and separators, is essential. This practice helps identify and address potential issues before they impact the efficiency and longevity of the equipment.
More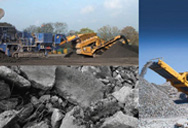
Analysis of Raw Mill Machines Maintenance in Cement Industry
IOP Conference Series: Materials Science and Engineering PAPER OPEN ACCESS Analysis of Raw Mill Machines Maintenance in Cement Industry To cite this article: R M Sari et al 2020 IOP Conf. Ser.: Mater.
More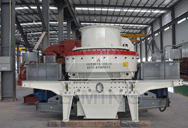
Operating and Maintenance of Electrostatic Precipitator in Cement ...
2018年12月1日 Cement plants aggravate the critical challenges of anthropogenic environmental pollution, global warming, climate change, and excessive fossil fuel use by emitting 15% of global contaminants.
More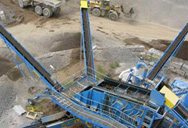
Everything you need to know about clinker/cement Grinding
For a cement mill: intermediate or outlet diaphragm. For the case of; cement mills with a drying chamber see raw mills. Mill working conditions: ventilation air speed through the mill. Bigger or smaller than 1.2 [m/s]. Material abrasivity. The [%] of slag or pouzzolana content on the fresh mill feed for cement grinding.
More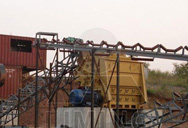
Review on vertical roller mill in cement industry its
2021年1月1日 The top 20 cement companies produces almost 70% of the total installed production capacity in the country. There are 210 large cement plants having total capacity of 410 MT cement production, with 350 small plants account for the rest. Out of 210 large units, 77 are situated in the states of Andhra Pradesh, Rajasthan and Tamil Nadu [13].
More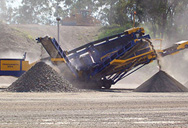
how to carry out maintenance of cement mill in cement.md
Navigation Menu Toggle navigation. Sign in Product
More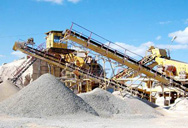
Vertical Roller Mill Operation in Cement Plant
The vertical roller mill (VRM) is a type of grinding machine for raw material processing and cement grinding in the cement manufacturing process.In recent years, the VRM cement mill has been equipped in more and more cement
More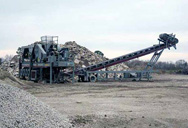
Optimization of Cement Grinding Operation in Ball
Feed material is ground in the ball mill, discharged and fed to a classifier with the help of a bucket elevator for classification of the ground cement into two streams – coarse and fines. The coarse fraction is sent back to the mill and the fines
More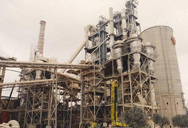
Everything you need to know about Automation and Optimization
In a cement plant wishing to reduce maintenance and sustainability of its systems, DC proliferation should be avoided or kept to a minimum. Open Control System (OCS) This system is based on a network concept methodology so as to avoid superordination by computer equipment to incorporate discrete instrumentation and logic functions.
More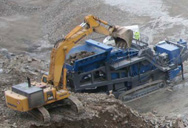
How to maintain vertical raw mill in cement plant?
2023年2月2日 To maintain a vertical raw mill in a cement plant, it is important to check the pressure and temperature in the mill regularly. ... Schedule regular maintenance shutdowns to inspect, ...
More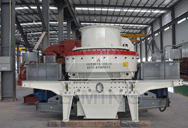
Heat Mass Balance in Cement Plant PPT Free Download
2021年11月27日 Heat Mass Balance in Cement Plant ... capacity of mill-300 TPH coal mill 2.0 NA 200 Running hr-20 in a day;1.58 kg gas/kg material, capacity of mill-38 TPH Pre-heater 6.8 1.50 8691 Out let Temp-280 degree ... Increased sealing capabilities Reduction in false air infiltration Low maintenance cost Reduces specific ...
More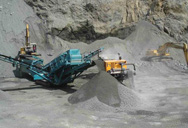
Cement Mill - Cement Grinding Machine AGICO Cement Grinding Mill
Coal mill is the main equipment in the pulverized coal preparation process.Because calcining top-grade cement clinker requires a stable supply of coal powder as the fuel of cement kiln, and more than 85% of pulverized coal should be finer than 200 mesh, water content less than 2%, and calorific value more than 6000Kcal/kg, therefore the pulverized coal preparation system is one
More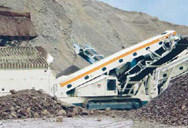
Optimizing Material Flow with Belt Conveyor in Cement Plant
2024年5月23日 Ensuring the longevity and safety of a belt conveyor in cement plant operations requires a comprehensive approach that includes regular maintenance, preventive measures, and robust safety protocols. By implementing these best practices, cement plants can enhance the efficiency and reliability of their conveyor systems while protecting their most valuable
More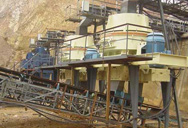
Operating and Maintenance of Electrostatic Precipitator in Cement ...
The cement process industries utilizing raw materials for the production of cement and these raw materials are burnt in the kiln at the temperature around 1400°C. During cement manufacturing process air gets pollute which includes particulate matter NOx, SOx., CO, CO2, hydrocarbons and other substances are released to the atmosphere. The burning of organic material such as
More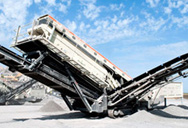
Reducing energy consumption of a raw mill in cement industry
Request PDF On Jun 1, 2012, Adem Atmaca and others published Reducing energy consumption of a raw mill in cement ... maintenance, and quality of ... The milling process quality evaluation can be ...
MoreArticle aléatoire
- les impacts environnementaux de l''exploitation miniere de minerai
- procedimiento del aspa molino
- machine de broyeur de déchets en béton rubble master
- faire broyeur à boulets crème utilisée
- concasseur de minerai gologique
- mines de calcaire riches
- bvl25 broyeur silencieux 2500w
- moteur utilisé par le moulin posho
- Petit concasseur de laboratoire
- britadores remco vsi 400
- Bahreïn Calcaire Concassage Machines
- tipos de maquinas trituradoras
- la machine de fraisage avec un cylindre de trou de tonalité
- Usine de micronisation pour des marteaux durs
- cuivre de conception affaissement broyeur a billes de plomb du minerai de zinc
- usine de transformation de fluorspar à vendre
- broyeur de pierres tamil
- viabilite de 200thp de concasseur pierre
- hammer crushers crusher
- usine de production d'énergie de broyage com fabricant
- concevoir un plan de mise en valeur du minerai de cuivre
- pieces de rechange kobe des concasseurs de malaisie inde
- tedi international sur la machine de concassage
- quipements de concassage allemand
- fondations de concasseur primaire secs
- machines d extraction d or alluvionnaire d afrique du sud
- du pulvérisateur
- Séparateur magnétique de minerai de fer rtifié en Turquie
- concasseur concasseur de
- Raison De Calcaire Broyeurs
- plan d affaires concasseur de carrière de granit en italie
- exploitation minière de concasseurs hydrauliques
- concasseur mobile en namibie charbon de russie
- données de production de concasseur canica vsi
- petit equipement minier concasseur à pierre
- vsi concasseur principe de fonctionnement nigeria
- Usine de concasseur de pierres de 100 tonnes
- Comment Vendre Concasseur A Machoires